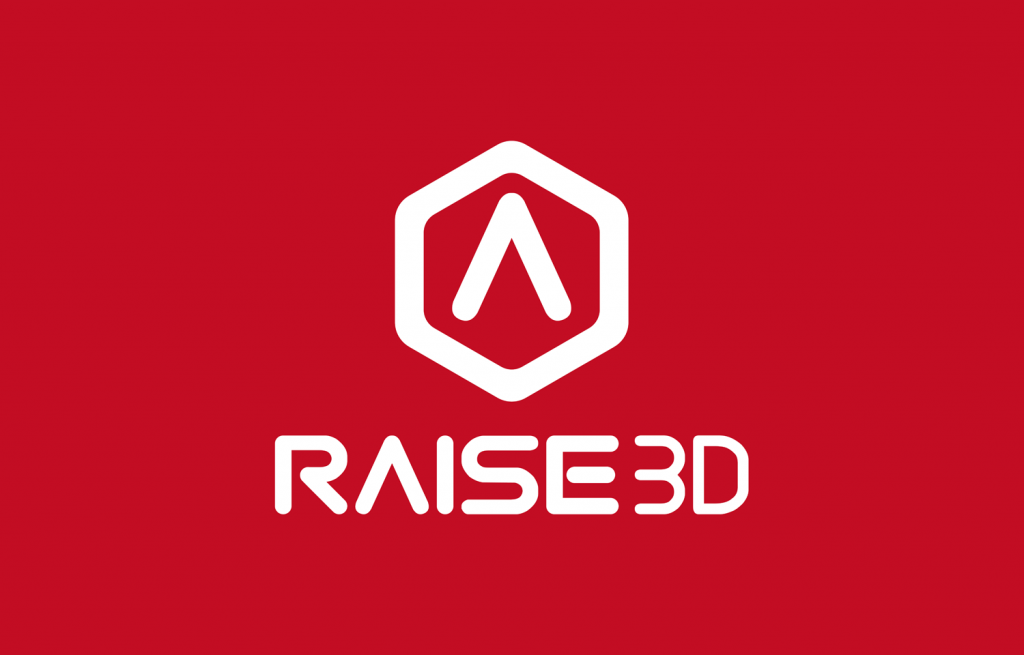
Modni trendi se spreminjajo hitreje, kot kdaj koli prej, zato se morajo proizvajalci bolj osredotočiti na maloserijsko proizvodnjo. Ta trend in prehod v proizvodnji vključuje tudi industrijo proizvodnje superg. Skoraj vsak večji proizvajalec čevljev raziskuje različne metode za doseganje hitrejših tržnih časov, ne da bi se pri tem soočal z izrednimi stroški izdelave orodij. Medtem ko večina sedanjih proizvodnih metod ne more zadovoljiti vse večjega povpraševanja po hitrejši maloserijski proizvodnji, 3D-tisk napreduje v smeri izpolnjevanja te potrebe. V letu 2020 je nekaj velikanov industrije proizvodnje superg uporabilo izdelke Raise3D, da bi naredili proizvodni preboj in dosegli še večji uspeh s 3D-tiskom.
Superge s 3D-natisnjenim zgornjim delom čevlja predstavljene leta 2020
Tradicionalna proizvodnja čevljev povzroča visoke stroške
V celotnem proizvodnem procesu superg zahteva proizvodnja zgornjega dela čevljev velike naložbe sredstev in časa. Glavni proizvodni postopek zgornjega dela čevljev predstavlja ravno pletenje, pri čemer sta vodilna primera te tehnike Nikejev Flyknit in Adidasov Primeknit. Stroj za pletenje, ki je potreben za obdelavo ravnega pletenja, je avtomatiziran in stroškovno intenziven kos obsežne opreme. Tovarna obutve se mora zanašati na veliko serijsko proizvodnjo s tako drago opremo, da lahko preživi na trgu. To pomeni, da se za proizvodnjo zgornjega dela čevljev uporablja na desetine ali celo na stotine pletilskih strojev, in sicer vsak dan in 24 ur na dan. Tudi za naknadno obdelavo, ki vključuje likanje in rezanje, je potrebno večje število delavcev. V povprečju en stroj potrebuje vsaj dva delavca.
HYPEBEAST. (Jan 30, 2015) Proces: Adidas Ultra Boost ali “Najboljši tekaški čevelj na svetu”. Youtube: https://youtu.be/4J_kxwT9zX4.
Čeprav lahko pletilni stroj deluje samodejno, njegovi rezultati še vedno vsakič potrebujejo precej naknadne obdelave. Pletilni stroj se napaja s poliestrskimi vlakni in izdela vse zgornje dele čevljev v enem samem deformacijskem listu. Sledita delovno intenzivno likanje in rezanje, da se pridobi raven in za uporabo pripravljen zgornji del. Če je zgornji del čevlja oblikovan z vzorcem, ki na površini ni pleten, so pri naknadni obdelavi potrebni dodatni koraki. Na primer šivanje in lepljenje je potrebno, da se material, kot sta usnje ali plastika, pritrdi na zgornji del čevlja.
Vir 1.: long xing, (10.5.2019) HIGH-PERFORMANCE 3 SYSTEM FLYKNITTING SHOE UPPER MACHINE, Youtube. , vir 2.: sneakerfactory.net.
Zaradi spreminjajočih se trendov je dobičkonosnost težja
V povprečju traja celoten raziskovalno-razvojni cikel novega izdelka najmanj 18 mesecev. Večina tega raziskovalno-razvojnega cikla je osredotočena na izdelavo prototipov zgornjega dela čevljev z uporabo običajnega postopka pletenja. Vendar pa se modne preference potrošnikov glede superg spremenijo vsaka tri leta, spreminjanje okusa pa bo v prihodnosti le še hitrejše. To na splošno pomeni, da je donosno obdobje za vsak nov izdelek krajše od leta in pol. Ker je obdobje donosnosti izdelka vse krajše, se zmanjšuje tudi celotna donosnost naložbe.
Implementacija aditivne proizvodnje z Raise3D
Podjetje Raise3D je razvilo inovativen FFF (Fused Filament Fabrication) postopek izdelave zgornjega dela obutve, ki se ga lahko računalniško prilagaja in popolnoma avtomatizira. Pri tem postopku se v 3D-tiskalnik neprekinjeno dovaja fleksibilno vlakno TPU (termoplastični poliuretan). Filament TPU se ekstrudira v obliki nitk na ravnem ležišču. Podobno kot pri pletenju tkanega tekstila tudi niti TPU sledijo vnaprej določenemu vzorcu. Nitke filamenta TPU se nalagajo druga na drugo in lepijo druga na drugo po programiranih navodilih, ki se posredujejo 3D-tiskalniku. V nasprotju s postopkom pletenja 3D-tisk takoj zagotovi celoten zgornji del čevlja z vsemi že uporabljenimi vzorci.
Digitalni postopek izdelave zgornjega dela čevljev v Raise3D
Rešitev podjetja Raise3D je digitaliziran proces, pri katerem so skoraj vsi parametri izdelave določeni z enim samim programom za razrez 3D datotek, ideaMaker. Delo z eno samo programsko opremo je omogočilo učinkovitejši postopek izdelave, kot če bi ga bilo treba kalibrirati za prilagajanje številnim vrstam strojne opreme in surovin. Poleg tega Raise3D ponuja tudi RaiseCloud, programsko opremo za upravljanje 3D-tiska v oblaku, ki se nemoteno in brezžično povezuje s 3D-tiskalniki Raise3D, da je upravljanje oddaljenega serijskega tiska še veliko lažje. Zmožnosti upravljanja RaiseCloud vključujejo pregled napredka tiska, spremljanje v živo, dodeljevanje nalog za tisk, nadzor tiskalnika, izmenjavo datotek in komunikacijo v skupini. Kombinacija strojne in programske opreme v ekosistemu Raise3D je tovarnam pomagala digitalizirati postopek izdelave zgornjega dela obutve tako z vidika upravljanja, kot izdelave.
RaiseCloud uporabniku omogoča oddaljeno upravljanje več tiskalnikov iz enega računalnika
Izboljšano prototipiranje s 3D-tiskom
Implementacija 3D-tiska s sistemom Raise3D je raziskovalno-razvojni cikel novega izdelka časovno omejila na 3 mesece, kar je v primerjavi s prejšnjim 18-mesečnim raziskovalno-razvojnim ciklom še posebej kratko. Vsak nov izdelek ima več modelov zgornjega dela obutve, ki jih je treba oceniti, preden se izbere najboljši model. Vsako zasnovo je treba večkrat prilagoditi in jo obilno vzorčiti. S postopkom Raise3D za izdelavo vzorca novega zgornjega dela obutve niso potrebna orodja za prilagajanje ali zahtevno programiranje. Preprost uvoz datoteke digitalnega dizajna in prilagoditev nekaj nastavitev v programski opremi omogoča 3D-tiskalnikom hitrer pričetek izdelovanja novih vzorcev.
3D-tisk zgornjih delov čevljev z Raise3D omogoča tudi tisk zgornjega dela čevlja z oblikovanimi vzorci tekstur, obrisov in okrasnih vzorcev na površini čevlja v enem samem tiskarskem opravilu. Zaradi prilagodljivosti tehnologije Raise3D lahko vizualni izgled čevlja deluje vzporedno z izkušnjo nošenja zgornjega dela čevlja. Zgornji del čevlja je lahko na primer tesnejši ali bolj elastičen. Ta dvojnost bo prihranila številne dodatne proizvodne postopke, kot so rezanje, šivanje in lepljenje. To pomeni, da bo postopek izdelave prototipa krajši, saj odpade preverjanje, ki je potrebno za izvedljivost množične proizvodnje.
Vzorci zgornjega dela čevlja z uporabo tehnologije Raise3D
3D-tisk je odličen za maloserijsko proizvodnjo
Vsi proizvajalci obutve potrebujejo manjše serije novih izdelkov za pilotne predstavitve na sejmih. V primeru podjetja Raise3D je lahko tovarna brez težav organizirala proizvodnjo majhne serije brez prenosa stroškov ali izdatkov za nabavo dodatnega materiala. Nekatere značilnosti 3D-tiskalnikov Raise3D med drugim vključujejo majhnost naprave, zmožnost samostojnega delovanja in izjemno prilagodljivost. Tovarna je z industrijskimi 3D-tiskalniki Raise3D lahko hitro izdelala nove zgornje dele čevljev v različnih izvedbah. Ti tiskalniki so samodejno delovali 24 ur na dan, da so dokončali zgornje dele čevljev za pilotno lansiranje.
FFF tiskalniki podjetja Raise3D so majhni in prilagodljivi
Prihodnost 3D-tiska
Pred leti, preden so proizvajalci začeli s 3D-toskom izdelovati zgornje dele čevljev, so nekateri že 3D-tiskali podplate in vložke. Odkar je 3D-tisk spremenil postopek proizvodnje copat, z namenom prilagajanja spreminjajočim se poslovnim potrebam in trendom, si je 3D-tisk izboril svoje mesto in je vsekakor tu dolgoročno. Raise3D je vzpostavil ekosistem za 3D-tisk, ki podjetjem in industrijam pomaga pri uvajanju aditivne proizvodnje. Ekosistem 3D-tiska je proizvajalcem superg omogočil prilagajanje, zadovoljitev povpraševanja po personalizaciji in omogočil proizvodnjo majhnih serij, kar postaja vse bolj mainstream.
Vir: raise3d.com.